The Port of Rotterdam and Maasvlakte 2 - PRINCE2 Case Study
Case Study

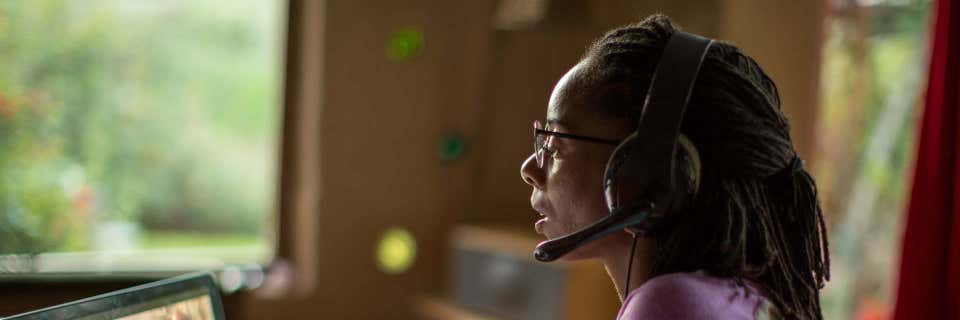
Case Study

- Case Study
- Project progress
- Project planning
- Project management
- PRINCE2
December 31, 2012 |
9 min read
- Case Study
- Project progress
- Project planning
- Project management
- PRINCE2
All of our White Papers and Case Studies are subject to the following Terms of Use.
A major step in Maasvlakte 2, a project first started in 2004, was reached a year ahead of schedule. On Wednesday, 11 July 2012 Her Majesty Queen Beatrix gave the sign to close the 11 km seawall around 2,000 hectares of new, man-made land. This case study provides the background to this huge £2 billion infrastructure project, which has employed 20,000 people, is now running ahead of time and remains within scope and is on budget - and explains how the use of PRINCE2 has made this possible.
This case study is also available in Dutch (PDF, 4.5MB).
Introduction
On Wednesday 11 July 2012, the map of the Netherlands changed for ever. Her Majesty Queen Beatrix& gave the sign to close the 11-km seawall around 2,000 hectares of new, man-made land jutting out into the North Sea. In doing so she gave the Port of Rotterdam, and the country, a new shape.
Thus a major step in the construction of Maasvlakte 2 – a project first started in 2004 – was reached a year ahead of schedule. The first of a multitude of ships will come into this huge new port facility in spring 2013.
This case study provides the background to this huge €2 billion infrastructure project, which has employed 20,000 people, is now running ahead of time, remains within scope and is on budget, and explains how the use of PRINCE2® has made this possible.
History
The Port of Rotterdam can trace its heritage back to the 14th century, when the present-day city of Rotterdam was a small town of around 2,000 inhabitants with some simple docks on the banks of the Nieuwe Maas river – one of the myriad of rivers in the Rhine-Meuse delta that reach the North Sea on this part of the Dutch coast.
Rotterdam’s early success can be credited to the building of a ship canal (the Rotterdamse Schie) around 1350. This allowed Rotterdam to become a local trans-shipment centre between Holland, England and Germany, and in turn provided the impetus for its growth into a maritime city associated with the Dutch East India Company, which was formed in 1602.
Expansion
By the middle of the 19th century, Rotterdam was already one of the largest port cities in the world, mainly because of the growth in trade between Germany and Great Britain. However, the increase in shipping traffic created a capacity problem. There were too many branches in the river delta, making the port difficult to reach, and there was a constant battle with natural silting-up in the Rhine-Meuse delta. This was resolved by building a ship canal called the Nieuwe Waterweg (‘New Waterway’), which opened in 1872, with a length of about 20 km (12 miles), providing a clear waterway for ocean-going vessels. As shipping and trade grew, the port spread to the south bank of the river to find space for expansion (see the orange section on the map).
In the years between the two World Wars, the port and harbour expanded to the west of the city (red sections on the map), along the side of the Nieuwe Waterweg. This in turn was followed by further extensions after 1946 and again after 1960 (dark blue sections). The greatest expansion, however, occurred in the decade between 1960 and 1970 (light blue section), when the huge area further west was developed as Europoort, an industrialized, extended series of harbours and basins that could handle the rapidly increasing trade and cargo shipping now using the Meuse and Rhine rivers. Through these rivers, Europoort was connected to the Ruhr area in Germany as well as to Switzerland, Belgium and France.
As a result of this rapid growth in both demand and capability, between 1962 and 2004 Rotterdam became the world’s busiest port. Although it has now been overtaken (first by Shanghai and more recently by Singapore), it remains the third-largest port in the world, and the largest in Europe, handling over 35,000 seagoing and 130,000 inland vessels each year.
Rotterdam’s entire port and industrial complex covers 10,500 hectares and is 40 km in length, stretching from the city itself to the Maasvlakte along the Nieuwe Waterweg canal.
The problem
Even though it does not provide employment on a scale to match its physical size, the Port of Rotterdam is nevertheless the Netherlands’ biggest economic engine.
Europe’s largest port has often come close to its limits during its history, as the bursts of expansion show. In 2004, the port was once again getting close to capacity. The trans-shipment of containers increased by 16% in 2004, to 8.2 million TEU,1 up from the previous year’s 7.1 million TEU. The port was expected to handle around 9 million TEU during 2005 and projections indicated that it could grow to 12 million by 2010.
Rotterdam had almost exhausted its space for any further increase in container trans-shipment, with only a few hundred hectares of rentable sites available. Moreover, these small sites were mostly situated a considerable distance from the sea. It was already obvious that more intensive use of the existing port site was the only way to absorb the increase in container trans-shipment up to 2010. But beyond that, new capacity would have to be found.
Unfortunately, in the early 2000s, the Port of Rotterdam was struggling with several issues. There was national concern, especially in the Dutch House of Representatives, about large infrastructure projects. This reflected public opinion, which had become increasingly negative because such big, costly projects always seemed to come in late, outside scope and over their already expensive budgets. There were also basic doubts about the benefits that such projects actually brought. None of this was helped by the first Maasvlakte project, started in the 1970s, which was over budget and was seen as poorly managed.
This was not a good climate in which to propose a major new project expected to cost several billion euros, especially with a Minister of Transport, Public Works and Water Management who appeared to have doubts about the real benefits that Maasvlakte 2 would bring.
However, by 2004, in a decision known as Key Planning Decision-Plus, the Dutch government agreed in principle that a major project called Project Mainport Development Rotterdam (PMR) should go ahead. This overall project would have three large sub-projects: the Maasvlakte 2 project would create new port sites and basins close to the North Sea; the so-called ‘750 ha’ project would construct and furnish a new wildlife and recreational area in the immediate vicinity of Rotterdam; and the ‘Existing Rotterdam Area’ project would bring about more intensive use of the existing sites within the city.
While central government would coordinate the PMR project, the three sub-projects would be managed by different parties. The Port of Rotterdam Authority would undertake Maasvlakte 2, the Province of Zuid-Holland would be responsible for the 750 ha project, and the Municipality of Rotterdam would manage the Existing Rotterdam Area project.
The Maasvlakte 2 project organization
The Maasvlakte 2 project organization was set up as a separate part of the Port of Rotterdam Authority. The organization was designed to prepare for the port’s expansion thoroughly, transparently and professionally, and then to commission its construction. The project organization would also keep its own financial accounts. The Port of Rotterdam Authority therefore established a Project Board especially for the project, with a Maasvlakte 2 Project Director who would be accountable to the Port of Rotterdam Authority’s Board of Management. A Tender Board consisting of external tendering experts would provide advice on the call for tenders and contracting. On request or on its own initiative, an Audit Committee would advise the Supervisory Board of the Port of Rotterdam Authority about the project. A Sustainable Development Advisory Group, consisting of leading specialists in this field, would examine possibilities for building, furnishing and operating Maasvlakte 2 in a sustainable way. There was also a User Sounding Group, which included representatives of the Port of Rotterdam Authority’s clients. This group would advise the project organization on the logistical and industrial wishes of future users.
The project plan
In June 2004, the Maasvlakte 2 project organization asked four project management consultancies to present their ideas about how a large project of this nature could be controlled in such a way that the recurrent doubts could be resolved and any prospective partners and stakeholders reassured.
One of the four organizations invited was Dr Richard Moret’s Ambition Group, based in Rotterdam, which made the case for using the PRINCE2 project management methodology. After serious initial doubts about PRINCE2’s suitability for such a large infrastructure project, the Authority’s Chief Executive, members of the Authority’s Procurement Office and the Maasvlakte 2 Project Director, Ronald Paul, decided that PRINCE2 would be tested by using its methodology to prepare the necessary project plan.
Time was short since the plan had to be ready within three months, by the end of September. With no time to prepare or offer any PRINCE2 training, Ronald Paul nevertheless confirmed on one Friday that, as from Monday, PRINCE2 would be used. And so it was that Richard Moret and his Ambition Group team arrived on the Monday to join the project organization. The immediate task was the creation of a project plan, but Moret set about the full PRINCE2 project initiation process. Over the next couple of months, Moret’s team provided the PRINCE2 process knowledge and the project team provided all the inputs.
In the circumstances, preparing a project initiation document (PID) was a perfect starting point, since the PID is designed to determine whether the project should be undertaken at all. Furthermore, any work on the PID needs to be preceded by the all-important business case. In resolving these two elements the team was coming up with the answers that the government and other partners and stakeholders needed. Initially there was resistance to using the new methodology because people felt they had been doing project management for many years. Moret had the support of the Port of Rotterdam Authority’s Board of Directors and Project Director Ronald Paul, and met with them weekly, but he also worked directly with everyone on the team so the process of introducing PRINCE2 was ‘bottom up’ as well as ‘top down’. He and members of his team sat alongside the quality managers, the planners and the risk managers on a daily basis. By working with everyone, the team was able to illustrate how PRINCE2 creates the necessary discipline and has the appropriate processes to get through such a large volume of work quickly. In the course of working together, the benefits of product-based planning became evident, with product descriptions, a product breakdown structure and a product flow diagram clearly defined and the attendant identification of activities, the length of time and effort involved, risk analysis and cost calculations all being an integral part of the process. Fairly quickly, members of the organization started to accept the benefits of using PRINCE2.
The business case was fleshed out as the team moved towards assembling the PID, because the costs and timeframe had to come from the project plan before the business case could be completed with its critical investment appraisal. The major risks also had to be identified from work done on the plan. As always with PRINCE2, once agreement was given, the PID would be frozen so that it could be used in the future to measure the success of the project, but the business case would be continually updated to ensure that the project remained viable. In the absence of formal training, Moret and his team were conducting full-time coaching on the job.
Next steps
Once the PID and business case, along with the investment appraisal, were completed, Moret focused on coaching the management team in how to manage a project using PRINCE2, in the hope and expectation that the project would be approved. At about the same time, the APM Group, the PRINCE2 international accreditation body, launched a PRINCE2 Maturity Model (P2MM) to enable organizations to check how mature they were in managing projects using PRINCE2.
Only accredited consulting organizations, like Moret’s Ambition Group, were able to conduct the relevant assessment. Moret felt confident that PRINCE2 was sufficiently embedded in the Maasvlakte 2 project organization for such an assessment of the organization’s maturity level to be undertaken, and he believed the assessment would help him identify areas where more work was needed. For this he used the P2MM, which has five levels of maturity. He was delighted to find that the organization was already at Level 2 and he was therefore able to get the APM Group to accredit the Maasvlakte 2 organization accordingly.
It also meant that he could make recommendations for further development in the use of PRINCE2 on the project. This included closer integration of time management, financial control, quality management and risk management. It also included improvements to the quality review process, interface management and more proactive risk management. Moret additionally wanted to further formalize the use of the business case and ensure that it would be continually updated when appropriate.
When formal PRINCE2 training began in 2006, those who had already been using PRINCE2 under the Moret team’s guidance saw the PRINCE2 foundation course simply as confirmation of what they were already doing. Moret had always been keen to illustrate how effective the tools that PRINCE2 provides can be, and he reiterated that PRINCE2 was a means to an end, not an end in itself.
A setback
Although the construction of a second Maasvlakte had received initial political approval in 2004, it was stopped in January 2005 by the Raad van State (the Dutch Council of State which advises the government and parliament on legislation and governance). In its ruling on the government’s decision to go ahead with the PMR project, the Council of State held that insufficient research had been conducted into various areas, especially the potential environmental impacts. The studies necessary to conduct the research would take several months.
So it was not until early September 2005 that the Dutch government finally approved detailed plans for the PMR. The government’s approval of the detailed plans allowed work to start on the three projects, but when construction itself could actually get under way still depended on the consent of the House of Representatives. In the event, it was not until 10 October 2006 that final approval was given to start construction in 2008, aiming for the first ship to anchor in 2013.
Also in September 2005, the financing of the overall project was assured when the Dutch state reached agreement to acquire a 25% interest in the Port of Rotterdam Authority in return for €50 million.
Following an irrevocable decision to construct Maasvlakte 2, the state would pay another €450 million to increase its shareholding to 331/3%. Hans Smits, Managing Director of the Port of Rotterdam Authority, was delighted with the state’s shareholding. ‘Given the port’s important role in the national economy, it is good for the state to be one of the shareholders,’ he said. ‘The chosen construction means the Port of Rotterdam Authority will get a €500 million injection of capital. We will use this money to build Maasvlakte 2.’
The project gets under way
The Maasvlakte 2 project organization was intent on avoiding some of the pitfalls that had befallen the original Maasvlakte project, where the site was built before space for terminals and facilities was sold. The revised plan was to start construction of the new land in 2008 and have the first container on the quayside in 2012. To achieve this and transfer risk to the marketplace, a twin-track approach was established.
In mid-2005, the Port of Rotterdam Authority invited container companies to express interest in having a site on Maasvlakte 2, and 15 of the world’s largest shipping lines and container trans-shipment companies put their names down. In September a call for tenders headed ‘Who will raise Maasvlakte 2 from the deep?’ was issued so that prospective contractors could register for the Design and Construct contract for the first and largest part of Maasvlakte 2. Companies experienced in building on water and/ or general contractors stood to win a contract that comprised the construction of sea defences, port basins, industrial sites and infrastructure.
As Project Director Ronald Paul said at the time: ‘Maasvlakte 2 is a complex project because it is business-case driven. We are expressly making allowances for clients’ wishes. We will not start building until we actually do have clients. The contractor we appoint will have to take their wishes and requirements into account, which calls for flexibility. What’s more, we want to be able to build faster if clients say they are in a hurry. But at the same time, we have to go through the prescribed licensing procedures. So we have to achieve the optimum between what the market wants and what the government prescribes. In addition, we have to deal with the incumbent business community and the shipping industry. We don’t want to obstruct their operations while construction is in progress.’
The important point was that the build would only be in response to clients actually committing – there was to be no rush to finish building, a process that could go on until 2020 or even 2030. Activity would increase or decrease according to market demand. For example, sites that were bought in 2007 are only now being constructed in 2012.
So 2006 was taken up with the process of negotiating with three consortia of dredging and construction companies qualified to build Maasvlakte 2 and simultaneously negotiating with and refining the candidates who wanted to operate from the site. Flexibility was being built in on both sides. The Port of Rotterdam Authority asked all the candidates wanting to build terminals to give a guaranteed volume of containers they expected to handle (incoming and outgoing) via Rotterdam for every year of the total period of operation.
Should this prove more or less favourable in practice, then a system of bonuses and penalties would come into force. If the terminal operator handled more than estimated, it would receive a discount on the (extra) port dues it would have to pay. Less throughput than estimated would lead to additional payment of a percentage of the ‘lost’ port dues.
A similar approach was taken with contractors. They were shown what was planned for 2020 and 2030 and what, for example, they would have to construct by 2020, but they were then given free rein in how they went about it. A special organization, called CMO1, would constantly review the quality of work of the suppliers, which would be paid according to the volume of stones or sand they brought in. CMO1 would check quality and then the quantity would be measured independently by a specialist organization, separate from the Port of Rotterdam. If it agreed the quantities, then suppliers’ bills would be paid within two weeks. The whole arrangement was designed to build in cooperative flexibility.
The plan with the terminal operators was to whittle the numbers down to a few candidates with whom the final negotiations could start, and then, in the second half of 2007, it would be possible to sign an agreement with one party so that the contractor could get down to work on the construction of Maasvlakte 2 in spring 2008. As Ronald Paul said, ‘Before we start building, in 2008, we will know precisely with whom we will be doing business at a later date. In our opinion, that is sensible business practice.’
At the beginning of 2008 it was announced that the PUMA consortium, consisting of the firms Royal Boskalis Westminster NV and Van Oord Dredging and Marine Contractors NV, would be building Maasvlakte 2 in the sea off the coast of the existing Maasvlakte. The work would comprise the construction of sea defences, the first port sites, some 3 km of quay and the roads and railways necessary to provide access to the Maasvlakte 2 area. The contract involved a total investment of some €1.1 billion. ‘Constructing a new piece of the Netherlands at one’s own risk in the busiest shipping area in the world is no small matter!’ said Ronald Paul. ‘And naturally, we want the entire operation to be sound in environmental terms, secure and ready on time, and at the end of the line we want to be charged the sum agreed upon in advance.’
Here are two artist’s impressions of Maasvlakte 2.
The end of Phase One
The closing of the seawall, signalled by Queen Beatrix, marked the end of the first phase of construction. At that point, around 215 million cubic metres of sand had been used. That is to say that about 90% of all the sand needed in the opening phase of the project was now in the right place. To the north and north-west lay the 3.5-km-long hard seawall, consisting of a stony dune and a block dam which was finished in February 2012. The structure is unique in the Netherlands, due to the combination of stony dune and block dam, for which almost 20,000 blocks of concrete from the seawall of the existing Maasvlakte were recycled.
The soft seawall in the west and south-west is 7.5 km long and consists of a beach with 14-m-high dunes. In 2011, the whole length of the dunes was planted with marram grass. On the south side, the beach has been made 100 m wider, so that beachgoers have a nice wide stretch of sand even when the tide is in. There are over 1,500 parking spaces and a permanent building for the lifeguards on top of the dunes. Around the perimeter of Maasvlakte 2 a road, railway line, cycle path, and cables and pipes for utilities have already been constructed.
The role of PRINCE2
The use of PRINCE2 has accelerated the planning and delivery of the project so far and the budget is well under control. Those working on the project are very supportive of PRINCE2 and, instead of seeing the regular maturity assessment as an intrusion, they see it as part of the annual process of optimization and continuous improvement.
The use of the original P2MM maturity model, and more recently P3M3, has helped the organization to develop PRINCE2 in the right way, and has kept the focus on using the methodology correctly over the past seven years. By annually auditing the organization’s use of PRINCE2 and making recommendations for improving its implementation, the right governance has been maintained and the maximum benefit achieved from using PRINCE2.
Every year the business case is recalculated – the project organization is currently using Business Case No. 7 and it remains valid despite the economic downturn.
Ronald Paul, Project Director of Maasvlakte 2, says: ‘Due to the project governance according to PRINCE2, the project is still within budget and time.’ Hans Smit, CEO, Port of Rotterdam, says: ‘The project governance was one of the key factors for the success of the project. After three-and-a-half years of hard work, the seawall closure is a milestone in Dutch history. The sea defence surrounding Maasvlakte 2 is closed and will protect 2,000 hectares of new Holland.’
The success of the project, costing €2.6 billion and involving 20,000 people, is attributed to excellent planning and governance, all managed to PRINCE2 standards.
Acknowledgements
Sourced by APMG and published by TSO on www.AXELOS.com
Our Case Study series should not be taken as constituting advice of any sort and no liability is accepted for any loss resulting from use of or reliance on its content. While every effort is made to ensure the accuracy and reliability of the information, TSO cannot accept responsibility for errors, omissions or inaccuracies. Content, diagrams, logos and jackets are correct at time of going to press but may be subject to change without notice.
© Copyright TSO. Reuse of this Case Study is permitted solely in accordance with the permission terms
A copy of these terms can be provided on application to AXELOS at Licensing@AXELOS.com