Focusing on pipeline construction products using PRINCE2 Case Study
Case Study

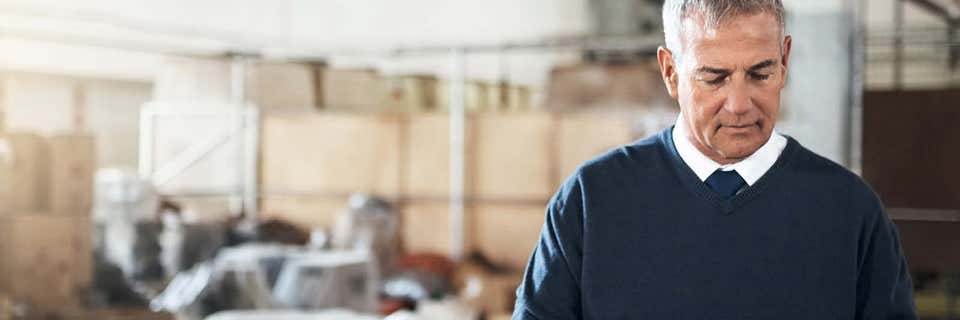
Case Study

- Case Study
- Project management
- Project planning
- Project progress
- PRINCE2
July 1, 2020 |
20 min read
- Case Study
- Project management
- Project planning
- Project progress
- PRINCE2
All of our White Papers and Case Studies are subject to the following Terms of Use.
Australian gas networks is one of Australia’s largest natural gas distribution companies. Having delivered gas to over 1.3 million customers, they completed a major project which involved constructing a new 300m diameter high pressure steel gas pipeline in the city of Brisbane.
This case study explores the entire process of constructing a pipeline and how PRINCE2 was utilized to deliver this project and tailor it to their own waterfall style method.
Introduction
Australian gas networks (AGN) is part of the Australian gas infrastructure group (AGIG), which owns and operates gas transmission and distribution pipelines across Australia. The AGN gas distribution networks deliver gas to over 1.3 million customers across Australia through approximately 25,000 kilometres of natural gas distribution networks and 1,100 kilometres of natural gas pipelines. AGN is one of Australia's largest natural gas distribution companies.
Australian Pipeline Association group is a leading Australian energy infrastructure business managing and operating a portfolio of assets of around $21 billion and delivering half of Australia’s natural gas usage. Along with the assets managed and operated by APA, the natural gas distribution networks are owned by its client, AGN.
APA recently completed a major project, (on behalf of AGN), by constructing a new 300mm diameter high pressure steel natural gas pipeline, a major feature of which included a 930-metre directional drill under the Brisbane River, in the city of Brisbane. The horizontally directional drilling operation included navigating riverbed formations, such as loose gravels, mudstone, and marine mud along with existing river features such as active jetty piles, river leases and remnants of a World War II destroyer wharf structure.
This case study details how the project utilized the PRINCE2 project management method which was tailored to the current organization’s waterfall style approach with concept, develop, plan, deliver and close for the design and construction of new pipeline under the Brisbane River.
The project had four main components to it:
- concept and detailed design
- construction activities to upgrade the existing above-ground facilities on both sides of the river
- construction activities for the directional drilling and pipe laying to link up with the above ground facilities
- commissioning of the new pipeline and upgraded facilities.
1.1 AIMS AND OBJECTIVES
APA Group aimed to achieve the following objectives:
- duplicate the existing pipeline under the Brisbane River which is an aging strategic asset for the client
- introduce improved gas supply metering facilities at the main metering station location of the pipeline
- provide improved and safer pressure regulation at the main metering station – protecting lower pressure assets downstream of the pipeline.
Concept and detailed design
Work began on the new pipeline proposal in October 2015, with the client requesting some options for the treatment of the existing pipeline which was deemed a critical aging asset.
Amongst the different options considered by APA and AGN to manage the gas supply risk, it was decided to duplicate the existing pipeline crossing.
With the preliminary station works completed by Summer 2016, the focus shifted to the new pipeline route with three options put forward for a discussion with the client, each of them with different costs and construction issues; they were also different in terms of risk to the security of supply from the existing pipeline crossing.
During the internal review in Summer 2017, a number of horizontal directional drilling contractors were approached to provide a budget estimation for the construction works and a consultation on the design. This provided an insight into the proposed project budget and confirmation that the concept design was fit for purpose.
Detailed design progressed with the river design and was finalized in April 2018, as shown in Figure 2.1. APA group sought third-party review, which the design successfully passed; this brought the successful completion of the first stage of the project.
Figure 2.1 Concept for Brisbane River Crossing options 1, 2 and 3 (Rennie, 2017)
Minimum quality specifications
The principal output from the project was to produce a new high-pressure steel pipeline, constructed to the current Australian Standards that could be operationally cleaned and internally inspected with the use of pipeline inspection tools.
For operational safety, the new pipeline was required to be adequately saturated with odorant to ensure the odorant level of the directly connected distribution network does not drop below 20% of the lower explosive limit (LEL). The steel has a level of porosity that would absorb residual odorant in the gas jet stream and in doing so, increase the level of LEL that any gas leak would be detected and exposing an unacceptable level of risk to the general public.
The project brief also required that the pipeline, station, and associated works, as well as being constructed to the current Australian Standards, did not impact on other underground public utility infrastructure, including electrical, telecommunication, water and sewer assets. To ensure there was no impact, the project liaised with other utilities regarding electrical high voltage and an aging critical asbestos water main. The project team worked closely with the affected utilities in finding suitable design options for the mutual benefit.
For added quality assurance during the construction and to reduce the time between construction completion and commissioning, two specific items were required from the construction contractor:
- Prior to testing and commissioning, internal inspection tools needed to be run through the pipeline with a minimum of 95% of the new pipeline internal diameter, to ensure there were no dents or internal welding products which could inhibit and/or damage computerized pipeline inspection tools, that could be run through the pipeline in later years.
- Regular manufacturer data records from the main construction contractor to be provided with a maximum of five days in arrears during the construction.
Another issue identified during the project was that the construction of the pipeline was under the flight path of the main Brisbane Airport. During pipeline commissioning, it was necessary to purge and flare natural gas. As a result, additional project quality specifications were in place to ensure there was no impact on the major domestic and international airport flights identified to have a flight path within vicinity of purge location. The project team ensured that during the commissioning process any flaring would not create additional lift to any approaching aircraft. They also worked with the civil aviation safety authority to determine the anticipated plume height and assisted in the notification to aviation authorities.
The project approach
The project approach included using PRINCE2 project management method, which was tailored to the current organization’s project management method waterfall style approach (concept, develop, plan, deliver, and close).
Breaking down the products to be produced by the project enabled the team to focus on each deliverable; in turn, identifying items that might not have been uncovered until the construction phase, which may have added costs to the project.
Quality assurance was an important factor in this project; with a significant amount of the pipeline to be under the river and the somewhat reduced ability to complete any post- construction repairs. The project team sought to ensure the construction information from the field was received before any line pipe was installed into the river bore.
Tracking quality control for contractual product delivery dates were recorded and tracked in a quality register.
Directing the project and managing stage boundaries were the themes we had adopted, which added further value to the project. Reports such as end stage reports, highlight reports, and exception reports were crucial in ensuring the project team and the project board had the correct information to make concise decisions at the appropriate time. The communication plan, which is shown in Table 4.1, provides an overview of the anticipated and expected communication style and stakeholder being engaged along with what information the stakeholder required to provide guidance as needed.
Communication type | Objective of communication | Medium | Frequency | Audience | Owner | Communication Deliverables |
---|---|---|---|---|---|---|
Kick-off meeting | Introduce the project team and the project. Review project objective and management approach. | Face-to-face | Once | Project sponsor Project team Stakeholders | Project manager | Agenda Presentation Meeting minutes |
Project team meetings | Review status of the project with the team | Face-to-face Conference call | Weekly | Project team | Project manager | Agenda Team leader reports Meeting minutes |
Steering committee meetings | Report in the status of the project to management including risk | Face-to-face Conference call | Monthly | Project sponsor Steering committee | Project manager | Agenda Presentation Meeting minutes |
Project progress reports | Report the progress of the project in the reporting period including activities, deliverables, milestones, budget, progress, schedule, issues, changes, risks, quality, HR, costs and issues | Monthly | Project sponsor Project team Stakeholders | Project manager | Project progress report |
Table 4.1 Brief of communication plan from APA Group project management plan (Warman, 2019)
Figure 4.1: Picture showing the right of way used for the HDD sting construction (Sykes, 2019)
Figure 4.2: Picture showing sting elevation over commercial drive during pull back activities (Sykes, 2019)
Figure 4.3: 5 times diameter hot rolled induction bend installed with corrosion protection wrapping installed prior to backfill (Sykes, 2019)
The construction would have been unsuccessful without the identification of the products produced along with the level of detail chosen in breaking down the products.
Focusing on products.
- A detailed survey for pipeline route and public utility property identification
- Survey deliverables
- Survey works to complete survey works to Australian Standard 5488 along with review of the dial before you dig (DBYD) records
- Survey deliverables
- Above ground facilities on either side of the river – brief of station products
- Barred tees
- Steel forged fittings
- Isolation valves
- Spiral wound with internal ring gaskets
- Galvanized studs and nuts only
- Seamless pipe
- Electrical isolations
- Electrical isolation joints to prevent voltage from below ground pipe entering the station.
- Pipeline trenching on either side of the river – brief of direct lay products
- 5 times diameter hot induction bends
- Line pipe
- Pipeline delivery receipt
- Welding Non-Destructive Testing
- Field joint coat preparation
- Field joint wrapping and testing
- Corrosion Protection location
- PUP avoidance
- Location of line pipe laydown.
- HDD River – brief of major HDD products
- Due diligence and accept design
- Location of line pipe laydown
- Location of HDD string construction and suggested construction techniques
- Suggested option for crossing of road and large commercial drive
- Field joint preparation
- Field joint coating and testing
- Pipeline gauge and hydro testing success factors
- Consideration for pipeline ballast during pullback
- 100% Non-destructive Testing (NDT) on bore string welds
- 100% visual examination
- Electrical drainage test post pull through to ensure coating integrity.
During the construction phase, some strict timelines for deliverables were implemented into the contract as shown in Table 4.2.
Clause # | Product | Business days prior | Business days post | Trigger |
---|---|---|---|---|
1.3 a v | MDR Index | 10 | ||
1.3 b 1vA | Condition report | 3 | On receipt of line pipe | |
1.3 d i | As laid plans | 10 | Post PC date | |
1.4 b i | HDD designs | 10 | 10 days prior to commencement of the works | |
1.4 b ii3 | Client transmission rep | 10 | Minimum notice of site representative prior to pull back | |
1.4 d iv | Final as laids | 5 | Prior to hydro testing | |
1.4 f iii | QA/QC documents | 10 | 5 | Progressive MDR 5 days in arrears - Specific item for coatings |
1.4 g i | Pigging requirement | Prior to hydro testing | ||
1.4 I iii | Hydro procedure | 10 | Prior to hydro testing | |
1.4 I viii | Hydro report | 2 | Post hydro testing | |
1.4 l iii | Pre-Mob client review | 15 | ||
1.8 g | Design obligation APA review | 10 | Receipt of documents | |
1.8 h | Design obligation resubmit | 10 | Reply of client | |
1.9 a x | Third party crossing procedure | 2 | Prior to crossing | |
1.9 a xvii | Pigging works plan | 10 | Prior to pigging work | |
1.9 c viii | Resto to landowner standard | 5 | ||
2.1 k | Design change HCC | 3 | Client review period on design changes only |
Table 4.2: Quality control triggers for product delivery during construction (Warman, 2019)
Why is quality important?
Knowledge on how we measure the quality of a completed product enables us to ensure the process, hold points, and contractual obligations or other measures. It seems simple; however, the exact opposite can apply in fluid situations and is heavily influenced by budget constraints.
5.1 How was the quality of the pipeline under a river measured?
For the project, some simple excel spreadsheets were created to track the number of document transmittals that were received from the design contractor. The contract was clear on the contractor deliverables and the response times required by APA for each deliverable.
During the project, APA received 373 individual documents over a total of 207 transmittals. On the surface this may seem small, however, without this simple quality assurance tool APA would not have met its contractual obligation due to balancing other workloads along with changes to the lands and engineering team members.
This tracking system was transferred into the plan and delivery phases for the construction contractor, allowing APA to directly influence the correct level of information within the tight delivery timelines.
Taking a leaf out of the PRINCE2 supplied templates and tailoring, the project team used a sheet to track the major product categories along with the individual products the designer, the project team or the constructor was to adhere to.
Project successes
The project has successfully been commissioned and handed over as an operational asset.
The project had several challenges, which have been summarized in the section below but was also a success. The seven PRINCE2 principles contributed to this:
- Continued business justification
- There were 6 regular weekly updates for the project board and monthly stakeholder meetings, therefore, the project maintained the business justification. During construction, the project team had fortnightly meetings with the construction vendor.
- Learn from experience
- The project learned from other projects, particularly the engagement with other public utility properties and seeking sanity proofing of the conceptual designs from other directional drilling subject matter experts.
- Defined roles and responsibilities
- The project took advantage of implementing a project board providing overall direction by allowing the project manager to manage the day-to-day activities as needed, along with the enforcement of the contract deliverables. To assist the project manager, the project provided additional support roles such as the construction superintendent and project engineer.
- Manage by stages
- The project broke the timeline into 3 distinct stages. This provided good visibility and control over the project and enabled the reporting up to the project horizon.
- Manage by exception
- Tolerances were built into the project such as delegation of authority limits (financial), variation approvals, contract executions and terminations along with acceptable timeline for completion deviations.
- Focus on products
- Focusing on the products along with the quality expectations gave exceptional control over the contractual deliverables. Product descriptions provided visibility for the project team on what we expected along with the critical timescales the products were due.
- Tailor to suit the environment
- The project tailored the deliverables, both contractual and internal, directly based of the complexity, technical difficulty, and strategic importance. The successful blending of the project board into the existing project method is an example of this. (Bennett, 2017)
The project has achieved the aims and objectives set down in the project brief and has led to the client happy with the outcome and the overall result.
Challenges
- Two different contractors were used for the design phase, and the construction phase which created challenges to ensure continuity between the two critical stages and also risk profile of the work was adequately addressed in the construction contract to be fair to both parties.
- The most critical sub-contractor, the HDD contractor, was changed prior to construction commencing which required an unplanned due diligence exercise to be required on the replacement HDD contractor.
- The steel pipe used for the project had been in storage for two years prior to construction commencement which had resulted in some slight corrosion being identified on the pipe ends of a number of pipes. This meant that some repairs were required as well as testing of the pipe coating to confirm its integrity.
- During construction, the first attempt at drilling under the river resulted in a broken drill rod which meant the entire drill string had to be abandoned under the river. The river directional drill profile had to be urgently redesigned.
- Due to the broken drill rod, a re-design needed to be issued within contract timelines (3 days) with specialist steering required to ensure accuracy to avoid the abandoned drill rods while still maintaining the new drill path within the required constraints (river leases).
- Temporary access agreements were required with a number of privately owned commercial properties to facilitate the construction work. As part of these agreements, it was necessary to allow owners access to their properties plus tight time constraints over which access could be granted.
- Certain engineering products were not recorded into the site plans adequately, this led to confusion on site.
- There was a change in project quality deliverables for the separation between the new pipeline and existing high voltage electrical cables. Amended depth of cover did not consider the rise in ground profile, making it difficult for the contractor to gradually bend the line pipe back to the design depth.
- The design of valve access chambers had inaccurate assumptions on the ground support and construction needed to install the valve.
- Staff management were juggling other non-dependent projects, which made time management for this project rather difficult.
- Quality change required for existing internal procedures for the commissioning of pipeline corrosion protection system.
- Organization does not formally support PRINCE2.
- Two different contractors were used for the design phase, and the construction phase which created challenges to ensure continuity between the two critical stages and also risk profile of the work was adequately addressed in the construction contract to be fair to both parties.
- The most critical sub-contractor, the HDD contractor, was changed prior to construction commencing which required an unplanned due diligence exercise to be required on the replacement HDD contractor.
- The steel pipe used for the project had been in storage for two years prior to construction commencement which had resulted in some slight corrosion being identified on the pipe ends of a number of pipes. This meant that some repairs were required as well as testing of the pipe coating to confirm its integrity.
- During construction, the first attempt at drilling under the river resulted in a broken drill rod which meant the entire drill string had to be abandoned under the river. The river directional drill profile had to be urgently redesigned.
- Due to the broken drill rod, a re-design needed to be issued within contract timelines (3 days) with specialist steering required to ensure accuracy to avoid the abandoned drill rods while still maintaining the new drill path within the required constraints (river leases).
- Temporary access agreements were required with a number of privately owned commercial properties to facilitate the construction work. As part of these agreements, it was necessary to allow owners access to their properties plus tight time constraints over which access could be granted.
- Certain engineering products were not recorded into the site plans adequately, this led to confusion on site.
- There was a change in project quality deliverables for the separation between the new pipeline and existing high voltage electrical cables. Amended depth of cover did not consider the rise in ground profile, making it difficult for the contractor to gradually bend the line pipe back to the design depth.
- The design of valve access chambers had inaccurate assumptions on the ground support and construction needed to install the valve.
- Staff management were juggling other non-dependent projects, which made time management for this project rather difficult.
- Quality change required for existing internal procedures for the commissioning of pipeline corrosion protection system.
- Organization does not formally support PRINCE2.
Lessons learned
Focusing on products and continued business justification ultimately set the project up for success and there were some major lessons learned. A well-prepared contract is critical to the success of a project, including clear terms and conditions and a clear scope of work. However, despite this, there can still be interpretation disputes within contracts and it is important to seek sound legal advice that is targeted on the specific issues.
Early engagement with external stakeholders is critical to project success, including external land holders and regulatory bodies, as their timelines and priorities are likely to be different to those of the project team.
In stage one, the learning experience was positive and valuable. During the concept phase, APA engaged with a local engineering firm to provide any existing geo-technical information on the riverbed formations around the location of the proposed drilling works. Fortunately, a number of other projects in the immediate area allowed APA to gain valuable knowledge of the riverbed make up without the need to complete additional geo-technical surveys. With this information, APA then requested feedback from local and international drilling providers for expert guidance on what soils formations should be targeted to achieve the complex drill arrangement.
During stage 2, the project team encountered a number of issues providing both positive and negative lessons. APA required the contractor to change the depth of cover from the tendered plans primarily due to the proximity to existing high voltage electrical cables. While the directional change of the pipeline was minor, there was budget and time impact from a previously unidentified disused sewer main. The re-design failed to consider the rising ground level, which did not allow for the contractor to reduce the pipeline depth of cover gradually.
Ultimately, this led to the pipeline construction having extra depth of cover for a longer distance than initially designed and the new pipeline was in direct impact with the disused sewer. A valuable lesson for the project team was to ensure the product descriptions detailed any need for the consideration of change in directions, especially in situations with varying ground levels.
A positive lesson learned was around the protection of the line pipe while it was in storage for over two years. The product description calls for the trilaminate coating (steel pipeline protective coating) not to be exposed to ultraviolet (solar radiation) for more than 6 months without some form of protection.
APA made use of the pipe supplier shade cloth tarpaulin for UV protection during storage. This ultimately worked well with minor coating cut back on 10 pipe ends of 142 pipes used. Focusing on the project product led to the elimination of the project risk.
In the final phase, the most notable lesson was introducing the gas odorant product into the pipeline during commissioning; natural gas is an odourless gas and requires the addition of a chemical odorant to provide the necessary smell for public safety. The regulatory requirements for odorant is that it must be detected at a level of at least 20% of the Lower Explosive Limit (LEL) of gas for operational safety of the new pipeline. Traditional methods call for injection of concentrated liquid odorant then flaring (burning the gas) during the commissioning activity.
Flaring would have introduced a concentrated plume (rising hot air) at the flare location, which would have created potential issues for the aircraft from the nearby airport. Furthermore, the severe drought conditions prevailing at the time, meant that fire ban restrictions were imposed, making flaring not viable in the conditions.
During stages 1 and 2, this issue had been unresolved because it was beyond the project horizon. The product description highlighted the need for consideration of the requirements form the airport. With minor changes to the process, APA completed the commissioning safely with manual and intentional slight overdosing of odorant to meet the regulatory requirements. Focusing on the product led to the solution.
Conclusion
Without the structure of a PRINCE2 method, the project may not have been successful. The structure provided a specific focus on the products and effective methods in managing each stage of the project.
The project was a success and met the requirements set in the project brief and to the satisfaction of the client. It was completed on time, within budget, and with all pipeline and station components including the corrosion protection (which was designed, installed and commissioned to Australian Standards).
About the author
Michael Warman is a project manager at APA Group has worked for APA for over 17 years. Michael has previously worked for gas and energy companies supervising the maintenance and construction of underground gas. He obtained his PRINCE2 practitioner status in October 2018.
References
Rennie, P 2017, Amendment 19992 - Holt St Crossing Plan A-C – Proposed (Figure 1), APA Group Brisbane, viewed 22 January 2020
Warman, M, 2019, Murarrie Looping Project Management Plan Stage 2 (Figure 2), APA Group Brisbane, viewed 21 November 2019
Sykes, G 2019, Project construction photographs (Figures 3, 4 and 5), APA Group Brisbane, viewed 15 December 2019
Warman, M, 2018, Product timing in contract (Table 1), APA Group Brisbane, viewed 10 December 2019
Bennett N, AXELOS 2017, Managing Successful Projects with PRINCE2® 6th Edition, AXELOS, viewed 21 November 2019